Understanding LOLER Meaning: A Key Element for Businesses in Home & Garden, Gardening, and Pest Control
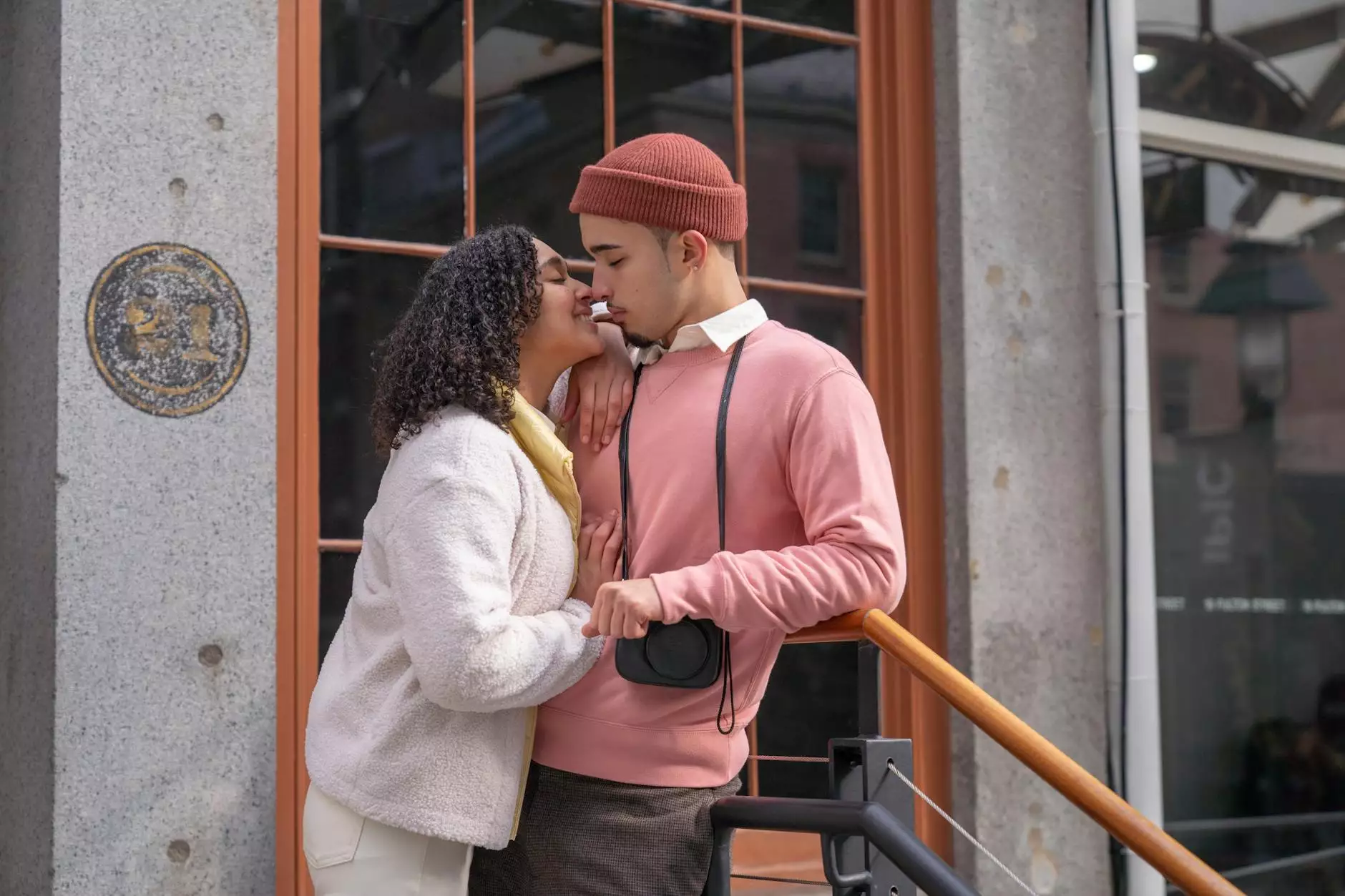
In the world of business, particularly in sectors such as Home & Garden, Gardening, and Pest Control, understanding safety regulations is paramount. One of the key regulations that businesses must be aware of is LOLER, which stands for the Lifting Operations and Lifting Equipment Regulations. This regulation ensures that lifting operations and equipment are safe and systematically maintained. The significance of LOLER meaning extends far beyond its definition; it directly impacts the various facets of operational practices within these industries.
What is LOLER?
The acronym LOLER refers to a set of regulations enacted in the UK to ensure the safe use of lifting equipment. The regulations require that all lifting operations are carried out safely, ensuring that any equipment used is fit for purpose and adequately maintained. Businesses must understand the implications of LOLER to ensure compliance and uphold safety standards.
Why is LOLER Important for Businesses?
Safety should always be a top priority in any industry. The importance of LOLER in business operations can be broken down into several key benefits:
- Enhanced Safety: The primary goal of LOLER is to protect employees and the public from accidents. By adhering to LOLER regulations, businesses can enhance safety in their operational environments.
- Legal Compliance: Non-compliance with LOLER can lead to legal repercussions, including hefty fines and potential imprisonment. Understanding LOLER meaning ensures that businesses stay within the law.
- Improved Efficiency: Properly maintained lifting equipment operates more efficiently. This efficiency reduces downtime and increases productivity.
- Increased Trust: Businesses that comply with safety regulations foster trust among employees, clients, and stakeholders, ultimately enhancing their reputation.
Key Components of LOLER
LOLER encompasses several crucial components that businesses in the Home & Garden, Gardening, and Pest Control sectors must understand:
1. Risk Assessments
Before any lifting operation, it is essential to conduct a thorough risk assessment. This assessment identifies potential hazards and outlines the necessary precautions to mitigate risks associated with lifting operations.
2. Equipment Inspection
Under LOLER, all lifting equipment must be inspected regularly. This includes checking for defects and ensuring that the equipment meets all safety standards. Businesses must maintain records of these inspections.
3. Operator Training
It is crucial that personnel involved in lifting operations receive adequate training. This ensures that they can operate lifting equipment safely and are familiar with LOLER regulations.
4. Maintenance Protocols
Regular maintenance of lifting equipment is mandated by LOLER. Companies need to develop and follow a rigorous maintenance schedule to keep equipment safe and operational.
LOLER in Practice: Sector-Specific Applications
The implications of LOLER meaning can vary somewhat depending on the specific sector. Below, we explore how LOLER principles apply across the Home & Garden, Gardening, and Pest Control categories.
Home & Garden
In the Home & Garden sector, lifting equipment might include hoists for garden materials, scaffolding for home renovations, or equipment for moving heavy items. Businesses must ensure that:
- All lifting equipment is suitable for its intended use.
- Regular risk assessments are performed to identify potential hazards.
- Staff is trained properly to operate lifting equipment.
Gardeners
Gardeners often utilize machinery and tools that require lifting. Adhering to LOLER is crucial for protecting those who maintain green spaces. Special attention should be given to:
- Inspecting equipment such as aerial lifts and lawn mowers.
- Implementing safety measures like proper lifting techniques.
- Continuous training for staff on safety procedures.
Pest Control
Pest control professionals frequently employ devices that may involve lifting to access certain areas or apply treatments. Key practices for compliance with LOLER include:
- Effective training on the operation of lifting load equipment.
- Substantial record-keeping for equipment maintenance and inspections.
- Reviewing and updating safety protocols regularly.
Challenges of Complying with LOLER
While the goals of LOLER are commendable, compliance can pose challenges for businesses. Here are some potential hurdles:
1. Cost of Compliance
Investing in equipment and training can be costly. Small businesses may find it particularly challenging to allocate sufficient funds for safety compliance.
2. Knowledge Gaps
Many businesses lack a comprehensive understanding of LOLER requirements. Training and resources must be made available to bridge this knowledge gap.
3. Documentation Challenges
Proper documentation is necessary for compliance. Many businesses struggle with maintaining comprehensive and accurate records of inspections and maintenance.
Best Practices for LOLER Compliance
To effectively meet LOLER standards, businesses can adopt several best practices:
1. Regular Training Sessions
Conducting regular training sessions ensures that employees are up to date with LOLER requirements and safety practices.
2. Develop a Compliance Calendar
Create a calendar that outlines when inspections, training, and maintenance should occur. This organization helps prevent lapses in compliance.
3. Engage Experts
Consulting with health and safety experts can provide clarity on compliance issues and help streamline operations to adhere to LOLER.
Conclusion: Embracing LOLER for a Safer Workplace
Understanding LOLER meaning and its implications for business practices in sectors like Home & Garden, Gardening, and Pest Control is essential for safety and efficiency. By implementing strict compliance measures, businesses not only protect their employees and customers but also foster trust and enhance their operational effectiveness. It is imperative to embrace LOLER not merely as a regulatory requirement, but as a critical part of a robust safety culture. Ensuring safety measures are in place will ultimately lead to improved business performance and employee satisfaction.
For businesses looking to succeed in these rapidly evolving sectors, comprehension of LOLER and its impact is not optional; it is a cornerstone of responsible and successful operation.