Understanding and Addressing Die Casting Defects
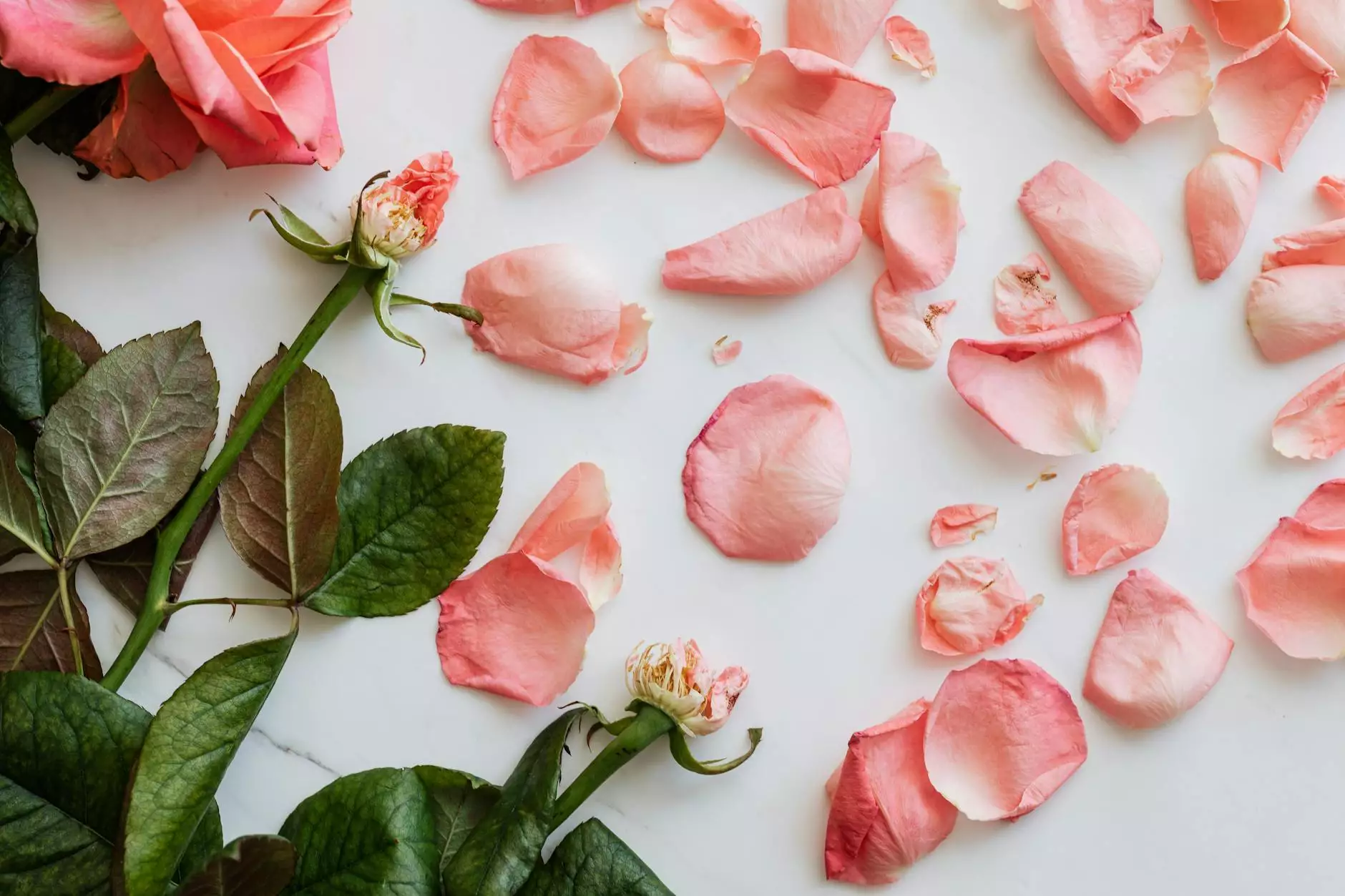
Introduction
Welcome to Wetron Industrial, a trusted name in the Home & Garden Appliances industry. In this article, we will delve into the world of die casting defects, exploring their causes, effects, and most importantly, how they can be addressed efficiently to ensure high-quality production.
What are Die Casting Defects?
Before we dive into understanding the causes and solutions, let's establish the concept of die casting defects. Die casting is a popular manufacturing process used to produce metal parts with intricate shapes and high precision. However, even with careful design and execution, defects can occur during this process.
Common Types of Die Casting Defects
There are several types of die casting defects that can impact the final product. Some common examples include:
- Porosity: This defect is characterized by the presence of small voids or air pockets within the cast metal, leading to weakened structural integrity.
- Surface Imperfections: These defects refer to irregularities such as cracks, warping, or rough spots on the surface of the cast part.
- Shrinkage: Shrinkage occurs when the material cools and solidifies unevenly, resulting in gaps or voids within the casting.
- Flash: Flash defects occur when excess material protrudes from the intended parting line of the die, leading to excess material wastage and potential quality issues.
Causes of Die Casting Defects
The root causes of die casting defects can vary depending on several factors. Some common causes include:
- Inadequate Die Design: Flaws in the die design, such as improper gating or venting, can lead to defects in the final casting.
- Inconsistent Melting and Pouring Temperatures: Temperature fluctuations during the melting and pouring stages can result in shrinkage or porosity defects.
- Metal Contamination: Impurities present in the raw materials used for die casting, such as alloys or additives, can contribute to defects.
- Poor Injection Parameters: Improper control of injection parameters, such as pressure, speed, or shot volume, can lead to defects in the cast.
Addressing Die Casting Defects
At Wetron Industrial, we understand the importance of addressing die casting defects to maintain the highest standards of quality. Here are some effective solutions:
Optimizing Die Design
By leveraging our extensive expertise, we design and manufacture precision dies that minimize the risk of defects. Through careful consideration of factors such as gating, venting, and cooling, we ensure optimal filling and solidification of the cast.
Process Optimization and Control
Our state-of-the-art facilities and cutting-edge technology enable us to monitor and control critical parameters throughout the die casting process. We maintain precise temperature control, injection parameters, and ensure consistent metal quality to eliminate defects.
Metal Quality Assurance
At Wetron Industrial, we strictly adhere to rigorous quality assurance protocols. Our stringent material selection and extensive testing procedures ensure that only the highest quality alloys and additives are used, minimizing the risk of defects arising from metal contamination.
Continuous Improvement Initiatives
We believe in a culture of continuous improvement and invest in research and development to stay at the forefront of die casting technology. By staying updated with the latest advancements, we continuously optimize our processes and practices to minimize the occurrence of defects.
Conclusion
Die casting defects can pose significant challenges to businesses in the manufacturing industry. However, with the right approach, expertise, and dedication to quality, such defects can be effectively addressed. At Wetron Industrial, we stand by our commitment to delivering the highest quality castings, free from defects, to meet the unique needs of our customers. Contact us now to learn more about our innovative die casting solutions.