Understanding Injection Moulding Tools: An Essential Component of Metal Fabrication
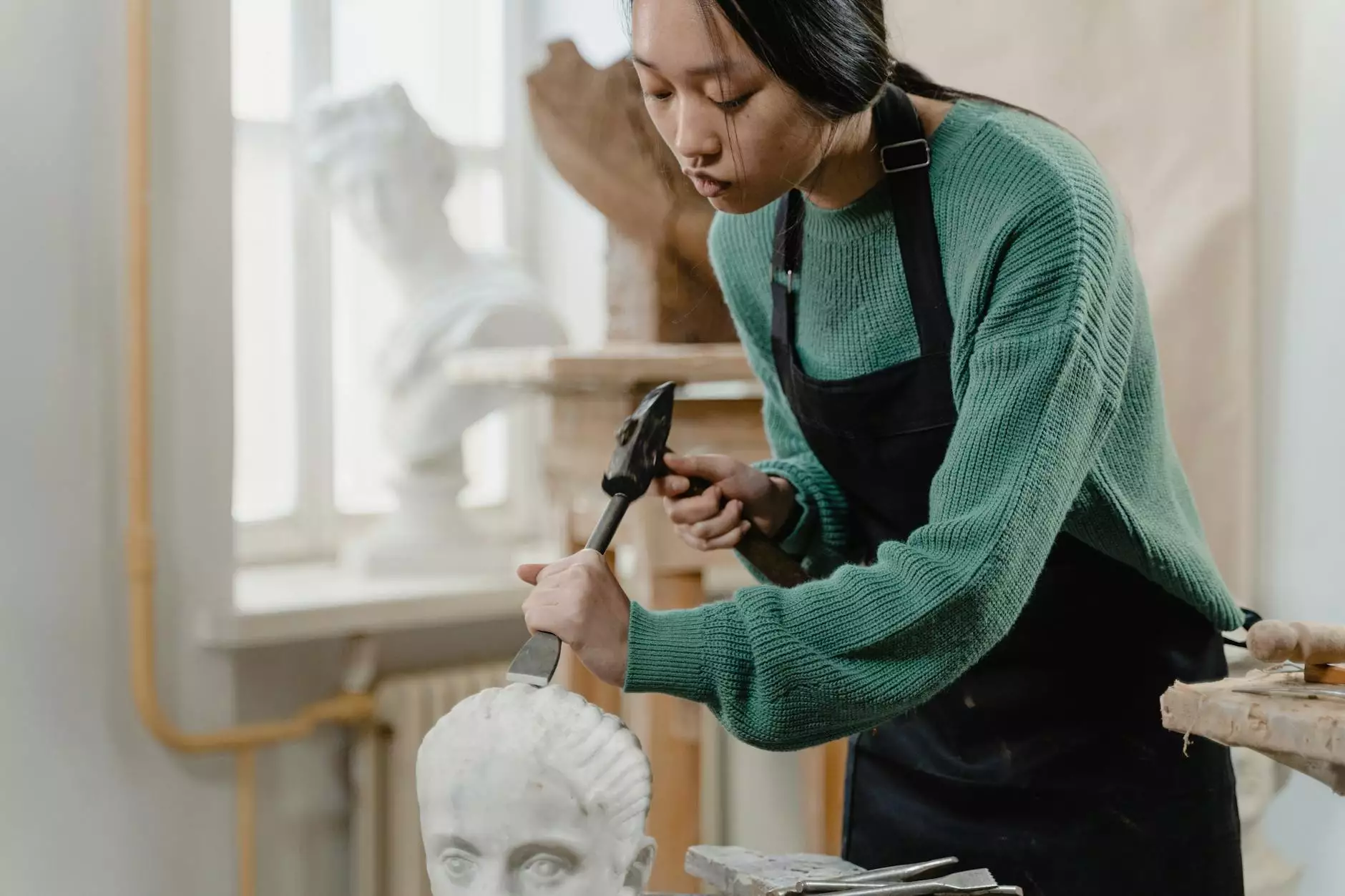
Injection moulding tools are a vital element in the manufacturing process, especially within the realm of metal fabrication. This comprehensive guide will explore the intricacies of these tools, their functionalities, advantages, and why they are critical for businesses in the industry, particularly for those associated with deepmould.net.
What is Injection Moulding?
Injection moulding is a manufacturing process used to produce parts by injecting molten material into a mould. This process is used for a variety of materials, primarily plastics, but it can also be adapted to metals in specific circumstances. The mould, which is a critical component, determines the shape and finish of the final product.
The Role of Injection Moulding Tools
The term injection moulding tools encompasses all the instruments and equipment necessary for creating a mould. These tools play a crucial role in ensuring that the moulding process is efficient, accurate, and cost-effective. Here are some key components of injection moulding tools:
- Mould Base: This is the foundation of the mould and provides the framework that holds everything together.
- Mould Cavity: The interior space where the material is injected forms the shape of the final product.
- Core and Cavity Inserts: These are the detailed components that shape the final item's features.
- Cooling Channels: These are essential for controlling the temperature of the mould during the injection process, ensuring the material solidifies appropriately.
- Injection Unit: This unit is responsible for melting and injecting the raw material into the mould.
Advantages of Using Injection Moulding Tools
The utilization of injection moulding tools comes with several advantages that elevate the manufacturing process:
- High Production Efficiency: Once the mould is created, parts can be produced quickly and in large quantities.
- Precision Engineering: Injection moulding tools allow for highly detailed and intricate designs, ensuring a high level of accuracy.
- Reduced Waste: The process is designed to utilize only the necessary amount of material, significantly reducing waste.
- Versatility: Different materials can be used, ranging from plastics to certain metals, making it adaptable for various industries.
- Cost-Effectiveness in Mass Production: Although the initial investment can be high, the cost per unit decreases significantly with larger production runs.
The Injection Moulding Process
Understanding the step-by-step injection moulding process is essential for anyone involved in metal fabrication. Here's a detailed look at the stages:
1. Material Preparation
The process begins with the selection and preparation of the raw material. Materials, usually in the form of granules, are chosen based on the desired properties of the final product.
2. Melting the Material
The chosen material is then heated in the injection unit until it reaches a molten state. This requires precise temperature control to ensure optimal fluidity and to maintain the integrity of the material.
3. Injection into the Mould
Once the material is melted, it is injected under high pressure into the mould cavity. The speed and pressure of injection can significantly affect the quality and finish of the final product.
4. Cooling and Solidification
As the injected material cools, it solidifies to take the shape of the mould. The cooling channels within the mould help facilitate this process, allowing for uniform cooling.
5. Ejection of the Final Product
After the material has solidified, the mould opens, and ejection pins push the finished part out of the mould. Careful handling is crucial to avoid damaging the product at this stage.
Applications of Injection Moulding Tools in Metal Fabrication
Injection moulding tools are highly versatile and find applications across various sectors within metal fabrication, including:
- Automotive Industry: Production of components such as dashboards, handles, and small structural parts.
- Consumer Electronics: Creation of intricate housings for smartphones, tablets, and other electronic devices.
- Medical Devices: Manufacturing of precise components for surgical instruments and diagnostic tools.
- Household Goods: Production of everyday items like kitchen gadgets and storage containers.
Choosing the Right Injection Moulding Tools for Your Business
Selecting the appropriate injection moulding tools is crucial for achieving the best outcomes in production. Here are some factors to consider:
1. Material Compatibility
Ensure that the moulding tools are suitable for the materials you plan to use. Different materials may require specific types of moulds with features like enhanced cooling systems or specialized coatings.
2. Design Specifications
Analyze the complexity of the parts you intend to produce. More intricate designs necessitate highly detailed moulds, so collaborating with skilled manufacturers can help achieve the desired functionality and aesthetics.
3. Production Volume
Consider the expected production volume. If you aim for high-volume manufacturing, investing in high-quality durable moulds will yield better returns in the long run.
4. Cost Considerations
Analyze the cost-effectiveness of the moulding tools within your budget. While higher-quality tools might demand a larger initial investment, they can result in significant savings over time due to increased efficiency and durability.
The Future of Injection Moulding Tools
As technology continues to advance, the field of injection moulding tools is evolving. Here are some of the emerging trends:
- 3D Printing: The integration of 3D printing technologies in creating moulds is becoming more commonplace, allowing for rapid prototyping and reduced lead times.
- Smart Technologies: Incorporating IoT and smart technologies into moulding processes can enhance monitoring and control, improving overall production efficiency.
- Sustainable Practices: There is a growing emphasis on creating eco-friendly moulding practices, such as using biodegradable materials and optimizing energy consumption.
Conclusion
In conclusion, injection moulding tools are indispensable in the metal fabrication industry. Their ability to enhance production efficiency, achieve precision, and reduce waste makes them a preferred choice for many manufacturers. By understanding their applications, selecting the right tools, and staying informed about emerging trends, businesses can position themselves competitively within the market.
For businesses looking for reliable and high-quality injection moulding tools, exploring the offerings at deepmould.net can be a great starting point. Embrace the future of manufacturing with advanced moulding practices and tools that meet your needs.